Induction Soldering Fiber Optic
Views Send Enquiry
Objective To heat a fiber optic housing to 400°F within 10 seconds for avsoldering application, to form a hermetic seal
Material Gold-plated aluminum housing, solder preform ring and flux
Temperature 400 ºF
Frequency 267 kHz
Equipment Power of 10kW power supply, remote heat station with a specially designed induction coil.
Process A specially designed, two-turn plate concentrator coil was used to provide uniform heat to the joint area. Initial tests were conducted to establish a heating pattern and time-totemperature.
The goal was to deliver uniform heat to the lid as well as to the housing. One solder preform was applied at the
joint and flux was applied to the joint surface. A ceramic fixture was used to maintain uniform pressure on the lid and keep it from buckling during the heat cycle. RF power was applied for 10 seconds, causing the solder to melt and flow.
Results Consistent and repeatable results were achieved with the Power of 10kW power supply and an 10-second heat cycle.
The solder flowed evenly and bonded the lid to the housing without any visible voids.
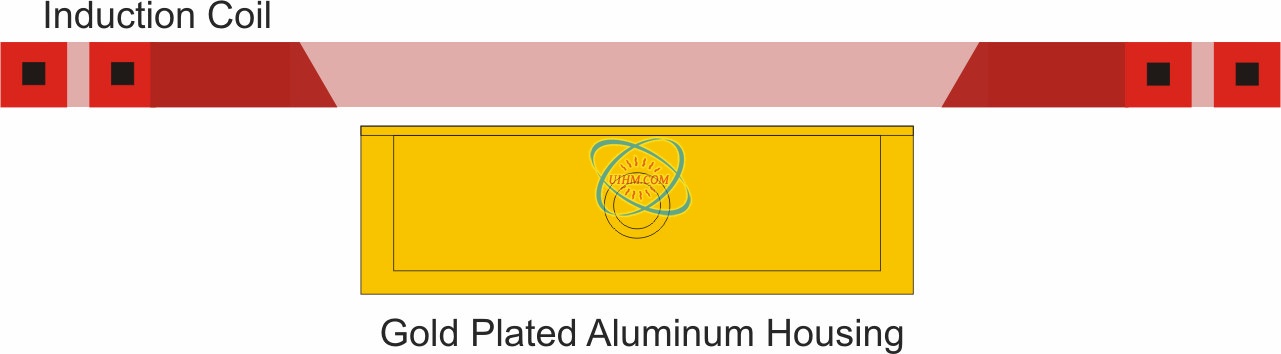
Soldering Fiber Optic
Related Content
induction brazing SS steel by handheld induction coil
induction melting silicon and steel
magnesium oxide acidic furnace for induction melting glass
induction preheating gas pipeline by full air cooled clamp induction coil and DSP induction heater
induction melting with Titanium alloy pot by customized induction coil
induction melting aluminium for casting wire wheel
induction heating steel plate by pancake induction coil
induction heating steel knife
Newest Comment
No Comment
Post Comment