Induction Heating carbon graphite anodes
Views Send Enquiry
Objective Heating carbon graphite anodes to destructively oxidize the parts to process embedded contaminants
Material anodes 2.5 x 2.5 x 4 (63 x 63 x 102) h x w x d in (mm)
Temperature 1900 °F 1000°C
Frequency 54 kHz
Equipment Power of 70kW induction heating system, custom multi-turn helical coil, 4 cap 1.0μF workhead
Process An air purge system is used to provide fresh air (~25 f3/hr) to the part during the heat cycle and to provide a swirling action for maximum contact with the surface of the anode.
The anode is placed inside the induction-heating coil and heated to a temperature of 1000°C. After 2.5 hours, the anode
burns to about 0.375 inch diameter piece.
A pyrometer/controller is used to provide constant temperature as the anode reduces in size.
Results/Benefits Induction heating allows this process to be very efficient and controllable
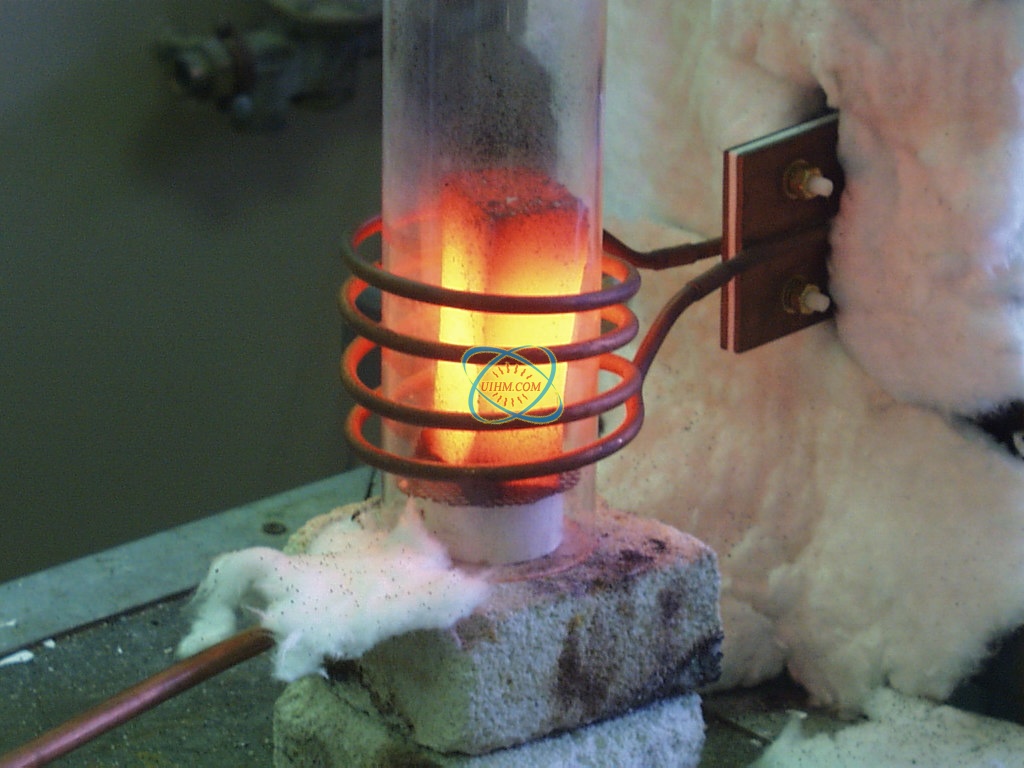
Heating carbon graphite anodes
Related Content
induction brazing SS steel by handheld induction coil
induction melting silicon and steel
magnesium oxide acidic furnace for induction melting glass
induction preheating gas pipeline by full air cooled clamp induction coil and DSP induction heater
induction melting with Titanium alloy pot by customized induction coil
induction melting aluminium for casting wire wheel
induction heating steel plate by pancake induction coil
induction heating steel knife
Hot
induction painting after induction bending for pipelines
induction heating steel plate
induction remove copper from aluminium
induction heating stator frame
induction heating graphite mould
difference between induction heating inner surface and outside surface of steel ring
induction heating steel pot bottom
induction heating for heat preservation
Newest Comment
No Comment
Post Comment