Induction Heating Engine Valve
Views Send Enquiry
Objective To heat the face of an engine valve head to 900°F and maintain the temperature for an extended time, high
temperature stress test.
Material Engine valve head (two sizes), temperature sensing paint
Temperature 900 °F
Frequency 223 kHz for large part; 271 kHz for smaller part
Equipment Power of 10kW power supply, remote heat station with one 0.66 mF capacitor, a specially designed, multiturn induction coil and an optical pyrometer.
Process A specially designed multi-turn pancake coil was used to provide uniform heat to the part. To provide optimum coupling, the face of the valve head was placed approximately 3/8” away from the coil. RF power was applied for 4 minutes to heat the larger valve to 900°F; the smaller valve head required 2 minutes to reach the same temperature. For closed-loop temperature control, the optical pyrometer was then used to maintain the temperature at 900°F.
Results Uniform and repeatable results were obtained with the UIHM power supply and induction coil at 900°F.
Depending on the part size, the correct temperature was reached in 2 to 4 minutes.
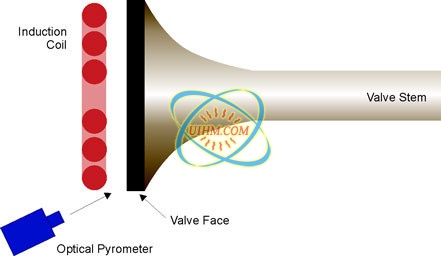
Heating Engine Valve
Related Content
induction brazing SS steel by handheld induction coil
induction melting silicon and steel
magnesium oxide acidic furnace for induction melting glass
induction preheating gas pipeline by full air cooled clamp induction coil and DSP induction heater
induction melting with Titanium alloy pot by customized induction coil
induction melting aluminium for casting wire wheel
induction heating steel plate by pancake induction coil
induction heating steel knife
Hot
induction painting after induction bending for pipelines
induction heating steel plate
induction remove copper from aluminium
induction heating stator frame
induction heating graphite mould
difference between induction heating inner surface and outside surface of steel ring
induction heating steel pot bottom
induction heating for heat preservation
Newest Comment
No Comment
Post Comment