汽车铸造技术的现状与发展趋势
次浏览
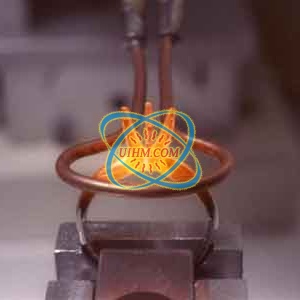
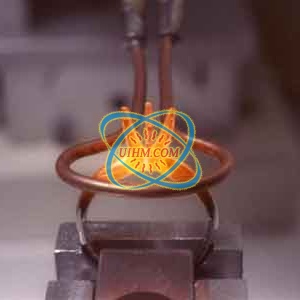
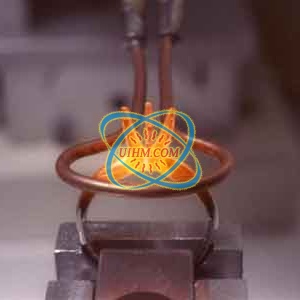
在科学技术迅猛发展的今天,由于铸造成形工艺的特殊优势,有些复杂结构件目前尚无其他制造工艺可替代。铸造工艺仍是最经济且便捷的金属成形工艺。随着全球经济一体化,在国际间的合作日益密切、竞争日趋激烈之时,中国汽车铸造业应更充分地发挥铸造资源优势,发展自己的铸造工业。
1. 中国铸造业现状
中国是当今世界上最大的铸件生产国家,据资料介绍,我国铸造产品的产值在国民经济中约占1%左右。最近几年,铸件进出口贸易增长较快,铸件的产量已达到9%左右。我国铸造厂点多达2万多个,铸造行业从业人员达120万之多。“长三角”地区的铸件产量占全国的1/3,该地区主要以民营企业为主,汽车和汽车零部件行业的发展有力地拉动了铸造行业的发展。万丰奥特是亚洲最大的铝合金车轮企业,年产值超过10亿元,出口额达6 000美元。昆山富士和机械有限公司生产汽车发动机和制动系统的铸件,年产量达4万t,销售收入5.5亿元。华东泰克西是一个先进的现代化气缸体铸件生产企业,具有年产1 00万件
轿车气缸体铸件能力。山西是铸造资源大省,有丰富的生铁、煤炭、铝镁、电力、劳力资源、使山西的铸造产业有得天独厚的优势,具有500个铸造企业,80%为民营企业。山西国际、河津山联、山西华翔年产量分别达4万t、2万t、12万t。“东三省”有一汽集团、哈飞集团等骨干汽车企业带动了汽车铸件产量的增长。一汽集团铸造公司,已经形成40万t铸件的生产能力。辽宁北方曲轴有限公司,到“十一五”末将形成年产15万台发动机、100万件曲轴、产值20亿的曲轴生产基地。“珠江三角洲”压铸行业发达,有700多个压铸企业,年产量达20万t。东风日产、广州本田、广州丰田和零部件企业有力带动了压铸业的发展,轿车气缸体、气缸盖的压铸件产量逐年增长。
2. 国外铸造业现状
近几年来,全球铸造业持续增长,2004年铸件产量比上一年度增长8.4%,中国生产铸件2242万t,全球排名第一,比上一年增长23.6%。全球十大铸件生产国的产量与增长率见表1。从表1可见,2004年中国的铸件产量约占全球铸件产量的1/4。巴西铸件产量增长最快,达到25.8%。增长率超过2位数的国家有巴西、中国、墨西哥、印度,都是发展中国家。而发达国家的铸件增长率普遍较低。美国铸件产量自2000年以来,已经退居到第2位。2004年美国铸件总产量为1231万t,其中灰铁件占35%、球铁件占33%、铸钢件占8.4%、铝合金件占16%。从需求上看,球铁铸件和铝铸件的需求在增长。2003年进口铸件占总需求的1 5%,进口铸件的价格比美国国内低20%~50%。近年来因铸造环保要求高、能源消耗大、劳动力昂贵等原因,美国大型汽车公司生产普通汽车铸件的铸造厂纷纷关闭,逐步将铸件的生产转向中国、印度、墨西哥、巴西等发展中国家。日本的铸造业不景气,其从业人员在减少。2004年日本铸件总产量为639万t,其中灰铁件占42%、球铁件占30%、铸钢件占4%、铝合金件占21%。从需求上看,球铁铸件和铝铸件的需求在增长。日本铸造界在技术创新方面作了大量工作,开发了球型低膨胀铸造砂、高减振铸铁材料、中硅耐热球铁等材料。其真空压铸的铸件能焊接和热处理,半固态铸造生产用于汽车铝轮毂,提高了强度和伸长率。镁合金压铸进一步发展,并取代重力铸造,其性能提高,成本降低。
3. 汽车铸造技术的发展方向
汽车技术正向轻量化、数值化、环保化方面发展。据有关资料报道,汽车自重每减少10%,油耗可减少5.5%,燃料经济性可提高3%-5%,同时降低排放10%左右。铸件轻量化主要有两个途径。一是采用铝、镁等非铁合金铸件,美国2003年统计有2/3的铝铸件用于汽车上,每车达到107 kg。二是减小铸件壁厚、设计多零件组合铸件,生产薄壁高强度复合铸件,并减少加工余量,生产近终形铸件。随着汽车技术的快速发展,为缩短铸件生产准备周期和降低新产品开发的风险,要求采用快速制模技术、计算机仿真模拟、三维建模、数控技术。而清洁生产、废物再生是铸造业的发展趋势,降低能耗是其持续发展的主题。我国汽车铸造业必须走高效、节能、节材、环保和绿色铸造之路,因为国家和社会要求严厉管控汽车铸造业的能源消耗大户和污染大户,以利改善铸造业热、脏、累的劳动密集型行业员工的劳动环境。
4. 汽车铸造技术发展趋势
国内外汽车铸造技术发展趋势很多,现仅简介一些在汽车行业大量流水线生产中的铸件技术及发展趋势。
4.1 砂型铸造成形技术
潮模造型经过手工紧实一震击+压实紧实→高压+微震紧实→气冲紧实→静压紧实几个发展阶段。静压造型技术的实质是“气中预紧实+压实”,其有以下优点:铸型轮廓清晰,表面硬度高且均匀,拔模斜度小,型板利用率高,工艺装备磨损小,铸型表面粗糙度低,铸型型废率低。因此,是目前最新、最先进的造型工艺,并已成为当今的主流紧实工艺。目前,高压造型和单一气冲造型已逐渐被静压造型所替代,原先高压造型线和气冲造型线的主机已逐渐更新为静压造型主机,新建铸造厂均首选采用静压造型技术。当前,国外比较有名的制造静压造型设备的厂家有德国的KW公司、HWS公司和意大利萨威力公司。国内汽车铸造厂家大都选用 HWS公司或KW公司制造的设备,如一汽铸造公司、东风汽车铸造厂、上海圣德曼铸造公司、华东泰克西、山西三联、广西玉柴、无锡柴油机厂等。
4.2 近净形技术
(1)消失模铸造成形工艺
消失模铸造也称气化模铸造、实型铸造、无型腔铸造。该工艺尺寸精度高达0.2 mm以内,表面粗糙度可达Ra5μm~Ra6μm,被铸造界誉之为“21世纪的铸造新技术”、“铸造的绿色工程”。该工艺方法是采用无粘结剂干砂加抽真空技术。据2003年统计,我国有150家企业用该工艺生产箱体类、管件阀体类、耐热耐磨合金钢类等三大类铸件,总产量超过10万t。国内汽车铸造厂,有的采用国产铸造生产线:有的采用简易生产线或单机生产;有的采用国外引进铸造生产线生产。一汽集团公司1993年从美国福康公司引进造型用振动台,生产 EPS模的预发泡机和成型机等设备,生产汽车进气管。长沙发动机总厂从意大利引进自动化铸造线生产铝合金气缸体、气缸盖铸件。合肥叉车集团用4段泡沫模片粘结成整体的工艺生产复杂箱体铸件,尺寸精度可达到 CT7-CT8级,产品出口美国。成都成工集团,用8块泡沫模片粘结成整体的工艺生产装载机变速器,铸件质量达320 kg,与砂型铸造比较,毛坯减重15%,成品率达95%以上。消失模工艺近几年在美国有较大的发展,通用汽车公司投资建造了6条消失模铸造生产线,大批量生产铝合金气缸体、气缸盖铸件。今后,该工艺将大量采用快速制模技术和模拟仿真技术,以缩短生产准备周期,实现铸件的快捷生产。未来的发展方向必定是质量好、复杂、精密、寿命长的高档模具。提高该技术的模具材料、成形工艺、涂料技术、工装设备的技术水平,使EPS铸件获得更广阔的发展前景。
(2)熔模精密铸造成形工艺
我国汽车熔模精密铸造技术有了长足的发展,采用近净形技术可以生产出无余量的铸造产品。熔模精密铸造工艺有水玻璃制壳工艺、复合制壳工艺、硅溶胶制壳工艺。汽车产品材料有碳素钢、合金钢、有色合金与球墨铸铁。国外有高合金钢、超合金材料。熔炼设备国内采用普通、快速中频炉;国外采用真空炉、翻转炉、高频炉技术。采用硅溶胶制壳工艺的零件表面粗糙度可达Ra1.6μm、尺寸精度可达CT4级,最小壁厚可达0.5~1.5mm。欧、美、日等国家开始关注精铸件在汽车业的应用与拓展。我国汽车用精铸件的市场需求量也在不断快速增长和发展,2003年精铸件的产量为60万t,产值达到110亿元。东风汽车精密铸造有限公司采用硅溶胶+水玻璃复合型制壳工艺,生产高技术含量、高附加值产品,将原来铸件、锻件、机加工及多件组装结构设计制造成一个整体精密铸件,显著降低了制造成本。
熔模精密铸造成形工艺将来的发展趋势是铸件产品越来越接近零部件产品,传统的精铸件只作为毛坯,已经不适应市场的快速应变。零部件产品的复杂程度和质量档次越来越高,研发手段越来越强,专业化协作开始显现,CAD、CAM、 CAE的应用成为零部件产品开发的主要技术。东风汽车公司、一汽集团公司的精铸企业作为中国精铸行业的领军者,一定能凭强大的研发实力和先进的技术快速发展。
4.3 制芯技术
目前,国内外汽车铸造制芯有3种制芯工艺,在现代汽车铸造中常并行采用的主要工艺有热芯盒制芯、壳芯制芯、冷芯盒制芯等,传统的合脂或油砂制芯已被淘汰。冷芯盒技术工艺有两个特点:一是硬化速度快,初始强度高,生产率高;二是砂芯尺寸精度高,可满足生产薄壁高强度铸件的砂芯。因此,制芯工艺技术有以冷芯盒技术为主的发展趋势。一汽铸造公司、东风汽车铸造厂、上海圣德曼铸造公司、华东泰克西、山西国际铸造公司等均采用冷芯盒制芯技术。
最先进的制芯工艺是结合锁芯(Key Core)和冷芯盒等技术的制芯中心,整个射芯、取芯、修整毛刺、多个芯子定位组合成一体、上涂料、烘干等工序,全部用一台或多台制芯机与机械手自动化完成。国外比较有名的制芯中心生产厂有西班牙LORMENDl公司、德国 Laempe公司和Hottinger公司、意大利的FA公司等。东风汽车铸造厂、一汽铸造公司、上海圣德曼铸造公司、华东泰克西、上海柴油机、洛拖二铁、潍柴、江西五十铃等均采用冷芯盒制芯中心技术。
4.4 铸铁熔炼技术
目前,国内外铸铁熔炼技术有两种主要方式:一是采用大型热风除尘冲天炉与工频保温炉双联熔炼工艺;二是采用中频感应电炉熔炼工艺技术。美国因达公司和彼乐公司生产的中频炉技术开始越来越受到重视,该技术日益成熟,其清洁、环保、节能、高效、安全的优势突出,是今后发展的方向。
因此,铸铁则由过去用工频炉熔炼逐步过渡到用高效省电的中频电炉熔化。一、汽铸造公司、东风汽车公司采用因达公司和彼乐公司生产的中频炉和保温炉技术,已经开发应用球化剂、孕育剂、蠕化剂和其他各种添加剂产品,形成商品化、标准化、规格化、系列化。铸铁孕育多用带光电控制的随流孕育机。新开发出的喂丝球化方法及其与
现代化检测技术相结合的SINTER CASTZ艺是铸铁球化及蠕化处理的一种很有优势的工艺,应用者日益增多。国外金属炉料经过破碎、净化、称量,大大提高熔化效率和铁水质量。国内的天津丰田、天津勤美达、苏州勤美达等铸造厂已对炉料采用破碎处理工艺。
最新评论
暂无评论
发表评论