感应加热容易控件控制局部加,因此在电子工业上有广泛的应用。半导体物质,硅太阳能电池,真空管的制造只是这种加热技术的一小部分应用。
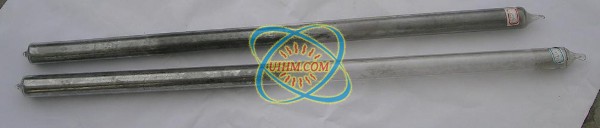
半导体提纯
制造半导体时,感应加热用来提纯。涂料和对晶体物质的处理。然而象锗和硅二极管,镓砷化合物等半导体具有高的电阻率,妨碍着直接感应加热。感应器的应用,与温度控制制相结合,为了电子工业提供了一定的益处。
例如,在对锗和硅二极管的处理中,物质首先必须提纯去杂。完成这个功能而应用的技术就叫提纯。这种提纯方法中,物质通过感应线圈时逐渐地熔化,因而产生一个窄小的熔化带。不纯物质留在窄小的熔化带中,比如渣是以易熔形式存在的。因此在能过线圈的范围时,它们被集中到棒的一端,熔化带被局限在加热线圈的范围内。加热物连接通过感应圈可进一步提纯产品。在操作中,一次通过多匝线圈与多次通过单匝的加热效果相同都可提供连续的窄小区域提纯度与通过熔化带的次数有关,实际上有一定的限度。据有关报导提纯度可达到含电活性杂质在亿万分之一以下。
在950摄氏度下处理锗二极管,可物物质放入碳感应器或船型器皿中渐渐通过感应圈。然而,当对硅提纯或镓砷化合物时,石墨感应器或船型器皿中的碳可污染产品。因此,采用一种叫做悬浮区提纯的方法。在这种技术中,必须保持棒的熔化带与表面扩散温度之间的平衡,因此,不需要船型器皿支撑熔化带。在悬浮带提纯法中,物质可通过线圈,或将线圈沿棒移动。熔化带温度1450摄氏度,结果将不纯物质集中在棒末端。因为硅具有高电阻,如果不升到一定温度,不能用450KHZ的电流加热。如果用超过3MHZ的频率则可直接加热,然而,用电阻法对硅预热可用450KHZ频率的装置加热。鉴于对带长的控制十分关键,并且须保持熔化带表厕所适当张力,在这种处理工艺中使用了了温度功率的闭环自动控制。
半导体晶体形成后,割成晶片,研磨擦光,用照像技术在晶体上多次曝光形成一定的电路,这些电路腐蚀入基表面,渐渐地腐蚀地区域形成硅的外层沉淀,或用cvd 化学汽相淀积,法形成一种 活性沉淀物。
外延沉淀包括将晶片放入石英管中的石墨磁化器加热的过程。温度上升到大约1350摄氏度,晶片上生有硅蒸气。硅在腐蚀区域处沉淀生成晶体结构。
超初,外延沉淀是在垂直的反应器中完成的所谓气流的方向,用的是一个扁平线圈制作的园盘形磁化器,这是因为基本上是批量处理,所以要求设计 一个系统,经济地处理在批的晶片,首先需要一个水平反应,在这里到系统中,使用一个大约为10.2*76.2*1.3的典型的石墨磁化器。主要考虑以下几方面
根据磁化器的厚度选定电源的频率(450KHZ)以获得最有效的加热。为了防止磁场 的抵消,感应器的厚度至少须是加热深度的三倍。为了减少下一工序的冷却时间,应尽量在有效的加热限度内减速小厚度。然后为了减速小温度梯度,厚度需要比深度大的多。
所需的功率并非主要由感应器的质量决定的,而更多的是由自由表面的辐射损失决定。1350摄氏度,这种 辐射线耗能是40KW/cm,对于上述规格的感应器全部耗能约69kW,外加10%为生成氢气的耗能。
为了进一步提高一次处理的品片数目,可用根形成盘形反应器。这里,晶片堆放在圆柱体状磁化器的周围。线圈均匀地绕在磁化器上,磁化器是类圆锥形的,以使气流充满整个表面。应用这种技术,可将磁化器的内壁(对感应加热目标而言)看作试管的一部分,因此只用10KHZ的频率就可满足这种规格磁化器的加热,而不存在场的抵消问题。
因为磁化器升温时,要从感应发生器吸收更多的能量,所以一大产啊分热容量是浪费的。为更有效地利用电动发电机装置,采用多工位加热站来利用过剩能量。然而对大多数固态电源来说是不可能的,因为它在一个时间内只能操作一个加热站。
最新评论
暂无评论
撰写评论