我国热处理的现状及发展方向
次浏览
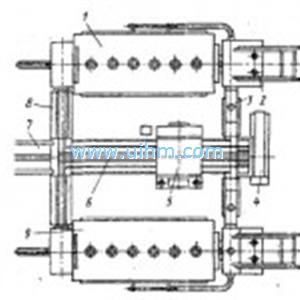
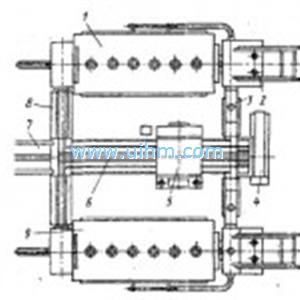
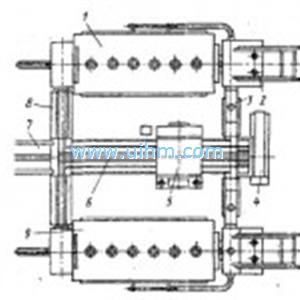
热处理对于充分发挥金属材料的性能潜力,提高产品的内在质量,节约材料,减少能耗,延长产品的使用寿命,提高经济效益都具有十分重要的意义。
建国以来,我国的热处理技术有了很大的发展,现有热处理生产厂点一万余家,职工15万人,专业科技人员约1000余人,热处理加热设备11万台,年生产能力660万吨钢件,年产值约50亿元,全员劳动生产率约3万元/人*年。目前我国在热处理的基础理论研究和某些热处理新工艺、新技术研究方面,与工业发达国家的差距不大,但在热处理生产工艺水平和热处理设备方面却存在着较大的差距,还没有完全扭转热处理生产工艺和热处理设备落后、工件氧化脱碳严重、产品质量差、生产效率低、能耗大、成本高、污染严重的局面。为促进我国热处理技术的发展,我们应全面了解热处理技术的现状和水平,掌握其发展趋势,大力发展先进的热处理新技术、新工艺、新材料、新设备,用高新技术改造传统的热处理技术,实现“优质、高效、节能、降耗、无污染、低成本、专业化生产”,力争到2000年时达到工业发达国家八十年代中期的水平。
1 大力发展多参数热处理和复合热处理工艺
传统的热处理,就主要控制的参数而言,多为常压下的温度时间两个参数的热处理;就工艺方式而言,多为单一的热处理。这样热处理的效果也只能是单一化。为此,要大力发展多参数热处理和复合热处理工艺 [1] 。
1.1 多参数热处理
(1) 真空热处理:这是一种附加压力的多参数热处理。它具有无氧化、无脱碳、工件表面光亮、变形小、无污染、节能、自动化程度高、适用范围广等优点,是近年来发展最快的热处理新技术之一,特别是在进行材料表面改性方面获得了很大的进展,许多新近开发的先进热处理技术,如真空高压气淬、真空化学热处理等,也需在真空下方能实施。采用真空热处理技术可使结构材料、工模具的质量和使用寿命得到大幅度的提高,尤其适合于一些精密零件的热处理。在工业发达国家,真空热处理的比例已达到20%左右,而我国目前约有真空热处理炉1200台,占热处理炉总数的1%左右,与国外的差距很大。预计今后随着热处理行业的技术进步和对热处理工件质量要求的越来越高,真空热处理将会有较大的发展。
(2) 化学热处理:这是一种附加成分的多参数热处理。普通化学热处理,如渗碳、碳氮共渗、碳氮硼共渗等,分别属于附加单成分、双成分和三成分的多参数热处理。近年来,又发展了许多利用新技术的新型化学热处理,如真空化学热处理,流态床化学热处理、离子渗金属、离子注入、激光表面合金化等,均可提高工件的耐磨损及耐腐蚀等使用性能。稀土在化学热处理中的应用(即与稀土共渗),能显著提高渗速,缩短处理周期,并可提高渗层的耐磨性和耐腐蚀性,这是我国的一大特色。此外,固溶化学热处理也是一个值得注意的动向,内蒙农机研究所黄建洪等人开发了含氮马氏体化处理(N*M处理)工艺,这是第一个以获得固溶N的含氮马氏体为目的的渗氮工艺,已成功地应用于剪毛机刀片生产 [2] 。
(3) 形变热处理:这是一种附加应力的多参数热处理。采用压力加工和热处理相结合的工艺,把形变强化和相变强化结合起来,使材料达到成型与复合强化的双重目的。形变热处理能提高材料的综合力学性能,并可以简化工序,利用余热,节约能源及材料消耗,经济效益显著。形变热处理的应用广泛,从结构钢、轴承钢到高速钢都适用。目前工业上应用最多的是锻造余热淬火和控制轧制。美国采用控制轧制来生产高硬度装甲钢板,可提高抗弹性能。我国兵器工业系统开展了火炮、炮弹零件热模锻余热淬火、炮管旋转精锻形变热处理、枪弹钢芯斜轧余热淬火等试验研究,取得了很好的效果。
1.2 复合热处理
复合热处理是将两种或两种以上的热处理工艺复合,或将热处理与其它加工工艺复合,这样就能得到参与组合的几种工艺的综合效果,使工件获得优良的性能,并节约能源,降低成本,提高生产效率。如渗氮与高频淬火的复合、淬火与渗硫的复合、渗硼与粉末冶金烧结工艺的复合等。前述的锻造余热淬火和控制轧制也属于复合热处理,它们分别是锻造与热处理的复合、轧制与热处理的复合。还有一些新的复合表面处理技术,如激光加热与化学气相沉积(CVD)、离子注入与物理气相沉积(PVD)、物理化学气相沉积(PCVD)等,均具有显著的表面改性效果,在国内外的应用也日益增多。
需要指出的是,复合热处理并不是几种单一热处理工艺的简单叠加,而是要根据工件使用性能的要求和每一种热处理工艺的特点将它们有机地组合在一起,以达到取长补短、相得益彰的目的。例如,由于各种热处理工艺的处理温度不同,就需要考虑参加组合的热处理工艺的先后顺序,避免后道工序对前道工序的抵消作用。
2 采用新的加热源和新的加热方式
2.1 新的加热源
在新的加热源中,以高能率热源最为引人注目。高能率热源主要有激光束、电子束、等离子体电弧等。高能率热处理就是利用高能率热源定向地对工件表面施加非常高的能量密度(10 3 ~10 8 w/cm 2 ),从而获得很快的加热速度(甚至能达到10 11 ℃/s),这样在极短的时间内(1~10 -7 S),将工件欲处理区的表层加热到相变温度以上或熔融状态,使之发生物理和化学变化,然后依靠工件自身冷却实现表面硬化或凝固,达到表面改性的目的。高能率热处理在减小工件变形、获得特殊组织性能和表面状态方面具有很大的优越性,可以提高工件表面的耐磨性、耐蚀性,延长其使用寿命。高能率热处理近年来发展很快,是金属材料表面改性技术最活跃的领域之一,其中激光热处理和离子注入表面改性技术在国外已进入生产阶段。我国一汽、二汽、西安内燃机配件厂等单位,都已建立了汽车发动机缸套的激光表面淬火生产线,但由于高能率热处理的设备费用昂贵等原因,目前我国尚未大量应用,但其发展前景广阔,今后将会成为很有前途的热处理工艺。
2.2 新的加热方式
在热处理时实现少无氧化加热,是减少金属氧化损耗、保证工件表面质量的必备条件,而采用真空和可控气氛则是实现少无氧化加热的主要途径。
在表面加热方面,感应加热具有加热速度快、工件表面氧化脱碳少、变形小、节能、公害小、生产率高、易实现机械化和自动化等优点,是一种经济节能的表面加热手段,主要用于工件的表面加热淬火。高能率加热具有加热速度快、表面质量好、变形小、能耗低、无污染等优点,也是一种极为有效的表面加热方式。在整体加热方面,有真空加热、高压加热、流态床加热等方式。流态床加热虽然能量密度不高,但加热快且均匀、工件变形小、表面光洁、处理后不需清洗、工艺转换容易、能提高产品质量、节能、公害小、成本低、并可以与化学热处理相结合,是一种很好的加热方式,特别适宜于多品种、小批量和周期性生产,可用来取代传统的盐浴热处理,其发展前景令人瞩目。
3 采用新的淬火介质和改进淬火方法
3.1 改进原有的淬火介质,采用新型淬火介质
淬火介质是实施淬火工艺过程的重要保证,对热处理后工件的质量影响很大。
正确选择和合理使用淬火介质,可以减小工件变形,防止开裂,保证达到所要求的组织和性能。
在热处理生产中,常用的淬火介质有水、油、盐类等,它们各有优缺点。例如,水是应用最广泛、最经济和冷却能力很强的淬火介质,但它在低温区冷却速度极快,易使工件变形和开裂;当水温超过40℃以上时,其冷却速度急剧降低,又易使工件淬不透。又如用油淬火,虽然对减小工件变形和开裂很有利,但对淬透性较差或尺寸较大的工件淬不硬,且油易老化,对周围环境的污染大,有发生火灾的危险。为此,要对原有淬火介质的性能进行改进,并积极开发应用冷却速度介于水和油之间、并可根据需要调整冷却速度,同时又经济、安全、无污染的新型淬火介质。
无机物水溶液淬火剂和有机聚合物淬火剂是新型淬火介质的发展重点,特别是有机聚合物淬火剂的研究和应用尤为引人注目,其优点是无毒、无烟、无臭、无腐蚀 、不燃烧、抗老化、使用安全可靠、且冷却性能好、冷却速度可调、适用范围广、工件淬硬均匀、可明显减少淬火变形和开裂倾向。从提高工件质量、改善劳动条件、避免火灾和节能的角度考虑,有机聚合物淬火剂有逐步取代淬火油的趋势,是淬火介质的主要发展方向,尤其是对于水淬开裂、变形大,油淬不硬的工件,采用有机聚合物淬火剂更是成功的选择。目前,世界上应用最多的是聚烷撑乙二醇(PAG类)淬火剂,它具有逆溶性,冷却速度在盐水和冷油之间,适用的淬火钢种范围广,使用寿命长。还有聚丙烯酸盐(ACR类)淬火剂、聚氧化吡咯烷酮(PVP类)淬火剂和聚乙基恶唑啉(PEO类)淬火剂等,也获得一定程度的应用。
多年来,我国在淬火介质的研究和应用方面,做了大量的工作,取得了一定的成绩,基本上满足了热处理生产的需要,但与国外的先进水平相比差距很大,并落后于热处理其它技术领域的发展,是热处理行业中的一个薄弱环节,今后应当给予重视和加强。
3.2 改进老的淬火方法,采用新的淬火方法
为了使工件实现理想的冷却,获得最佳的淬火效果,除根据工件所用的材料、技术要求、服役条件等,来合理选用淬火介质外,还需不断改进现有的淬火方法,并采用新的淬火方法。如采用高压气冷淬火法、强烈淬火法、流态床冷却淬火法、水空气混合剂冷却法、沸腾水淬火法、热油淬火法、深冷处理法等,均能改善淬火介质的冷却性能,使工件冷却均匀,获得很好的淬硬效果,有效地减少工件的变形和开裂。
4 研制开发各种新型热处理设备
热处理设备是实现热处理工艺的基础和保证,直接关系到热处理技术水平的高低和工件质量的好坏。我国热处理设备的生产已有40年历史,现已具备一定的规模和能力。最初是仿苏四、五十年代的在空气中加热的电阻炉,并以箱式炉和井式炉为主。七十年代对主要炉种进行了整顿,品种规格有所增加,性能有所改进,系列化程度有所提高。八十年代又进行了一次产品更新换代,发展了第二代节能系列产品,能生产多用炉、真空炉、离子渗氮炉、流态粒子炉等新型炉种 [3] 。自改革开放以来,通过引进国外先进的热处理设备和中外合资合作生产,使我国热处理设备的设计制造水平和生产能力有了很大的提高。我国现有电炉厂180多家,已形成年制造热处理炉9000台的能力。少无氧化热处理技术可以改进产品质量,提高生产率、降低成本,并可减少污染、易于实现自动化,其普及程度已成为当代热处理技术水平的主要标志,工业发达国家早在60年代就已基本淘汰了空气加热炉,实现了少无氧化热处理,而我国目前生产用的热处理设备大多还是箱式或井式电阻炉,90%以上系周期性作业,空气加热炉占热处理炉总数的70%以上,而可控气氛炉和真空热处理炉的比例只有5%左右。这些落后的热处理设备大都存在着炉温均匀性差,工件氧化、脱碳严重,设备的可靠性较差,配套仪表、元器件质量不过关,工艺过程控制水平低,产品质量不稳定,热效率低,能耗高等问题。因此,要对落后的热处理设备进行更新改造,努力提高电阻炉炉温的均匀性和其它工艺参数的控制精度,以保证和提高热处理工件的质量,并限期淘汰一批产品质量差、能耗高、污染严重的落后设备。要大力发展感应加热和无氧化加热技术,大幅度增加可控气氛炉和真空热处理炉的比例,逐步取代现有的箱式炉和井式炉,这是热处理行业技术改造的重点之一。在我国现实情况下,应大力开发和推广应用低真空多用炉,以提高产品质量,适应企业小批量、多品种的生产需要,这可能是一条适合我国国情、发展新型高效热处理设备的捷径。其它新型热处理设备,如离子热处理炉、流态粒子炉、激光热处理装置、电子束热处理装置等,也应积极开发应用。
需要指出的是,热处理设备的设计制造应与热处理工艺密切结合,热处理设备要能满足热处理工艺的要求,提高热处理的质量;同时,要根据热处理新工艺发展的需要,研制开发新型高效热处理设备,用热处理工艺来促进热处理设备的发展。要不断提高我国热处理设备的设计制造水平,增强自我开发和技术创新能力,这对提高热处理炉的性能、节约能源、提高生产效率、降低工艺成本,是十分重要的。热处理炉型要多品种、多规格,并尽可能采用相应的国际标准,要有温度均匀性指标(对于可控气氛炉还要有气氛均匀性指标),要提高国产元器件和检测仪表的精确度和可靠性,加强产品的质量检验,从而提高热处理行业的整体水平和经济效益。
5 加强新材料与热处理工艺的紧密结合和相互促进
5.1 低碳马氏体及其应用
低碳马氏体是低碳低合金钢经强烈淬火急冷后得到的一种显微组织结构,具有优良的综合机械性能以及良好的冷加工性和可焊性。近二十年来,我国开展了低碳马氏体及其应用研究工作,取得了很大的成绩。例如,低碳马氏体的强度比中碳调质钢高1/3以上,且综合性能良好,用来代替某些中碳调质钢(如高强度螺栓等),可使构件重量成倍减轻;低碳马氏体还具有很高的耐磨性能,可用来制造某些要求耐磨性好的零件(如拖拉机履带板等)。总之,低碳马氏体在石油、煤炭、铁道、汽车、拖拉机等部门应用广泛,收到了提高性能、减轻重量、延长使用寿命、简化工艺、节约能源、节约合金元素、降低成本等技术经济效果。
5.2 空冷贝氏体钢
贝氏体钢能够空冷自硬,并将冶金热加工工序与产品成型制造工序相连接,具有良好的强韧性配合、生产工序简单、节约能源、污染少、成本低等优点,因而引起广泛的重视。至今国际上空冷贝氏体钢系列有两类:一类是以英国P.B.Pickering为首于50年代发明的Mo-B系贝氏体钢,但因钼的价格昂贵而使其发展受到限制;另一类是以我国清华大学方鸿生教授为首于70年代初期发明的Mn-B系贝氏体钢,现己发展有低碳、中低碳、中碳、中高碳系列十多个钢种,应用到耐磨钢球、衬板、齿板、冲击锤、刮板、截齿、离心铸管、汽车前轴、连杆、液压支架等 [4] ,取得了很好的技术效果和显著的经济效益,成为贝氏体钢发展的重要方向。目前我国Mn-B系贝氏体钢己达到年产15万吨的规模,在“九五”末期将达到70万吨/年,占到全国特殊钢产量的5%~10%。
5.3 无莱氏体高速钢
大连铁道学院戚正风教授等研制成功无莱氏体高速钢,其合金元素与一般高速钢相同,碳含量则降低到钢水凝固时不形成共晶碳化物(莱氏体)、而又能在淬火回火后整体具有足够的强度、韧性与硬度的水平。这种钢加工成刀具后,通过渗碳,使表层得到≥70HRC的高硬度和600℃4 次回火后仍能保持67HRC的红硬性,同时得到55HRC高强韧性的心部,可使刀具使用寿命提高几倍 [5] 。
5.4 奥氏体-贝氏体球墨铸铁(A-B球铁)
70年代我国与美国、芬兰等国家同时研制成功A-B球铁,并获得了实际应用,由于A-B球铁既具有较高的强度和硬度,又具有良好的塑性和韧性,因而被广泛用于汽车、拖拉机、内燃机的齿轮、连杆、轴类等结构件以及矿山磨球、锤头等耐磨零件。80年代以后,国内外又从A-B球铁化学成分与热处理工艺两个方面深入进行研究。前者通过提高合金成份来得到铸态A-B球铁,以期取消成本高、工效低的等温淬火工艺;后者则努力完善热处理工艺,提高机械化和自动化水平,以提高生产效率。
6 重视热处理节能和环境保护
6.1 大幅度降低热处理的能耗
热处理是机械制造业中耗能最多的工艺之一,在工业发达国家,热处理生产成本的25%~40%是能源成本。
据统计,我国的热处理设备中,电炉约占90%,装机总容量约为600万Kw,热处理的年用电量近90亿Kw . h。由于我国的热处理工艺和设备比较落后,能源利用率低,热处理能耗水平为500~1000Kw . h/t,比工业发达国家多2~3倍,因此节能的潜力很大。热处理节能的途径主要有:(1)在热处理工艺方面,改进老工艺,推广应用先进的节能新工艺;(2)在热处理设备方面,改造或淘汰耗能高的落后设备,发展新型高效节能的新设备;(3)在生产组织管理方面,合理组织热处理的批量生产,力求集中和连续性生产,不断提高热处理的专业化生产水平。而搞好热处理,努力提高热处理质量,延长工件的使用寿命,则是最大的节能。
开发和推广应用非调质钢,是80年代热处理节能技术的一项重大进展。应用非调质钢,不仅能显著节能,而且减少了生产工序,节省了材料消耗,降低了成本,还可避免淬火时带来的变形和开裂,提高了工件的质量和使用寿命。目前,非调质钢多用于取代调质碳素结构钢,今后的发展趋势是用非调质强韧钢来取代调质合金结构钢,进一步扩大非调质钢的应用范围。
6.2 高度重视热处理生产的环境保护
热处理生产对环境造成的污染很大,包括排出的废气、废水、废液、废渣、粉尘、噪声、电磁辐射等,且随着生产的发展,其危害也日益严重。研究和采用无污染、无公害的热处理技术,并对排放的有害物质进行有效控制和综合治理,是消除热处理污染的主要措施。
1989年联合国环境署决定在全世界推行清洁生产技术。所谓清洁生产技术,就是通过对生产过程和产品的综合防治,减少废弃物产生,最大限度地保护自然环境和利用自然资源,即选取清洁的原料,采用清洁的工艺,实现清洁的生产过程,制造出清洁的产品。日本东京金属技术研究所金武典夫博士通过分析引起全球性的温室效应、空气污染、酸雨等对环境造成的影响,提出了一种“节能-高效-环保型热处理”的综合体系,它包括了预处理、热处理、后处理、技术保证体系和环境管理体系,而其关键是将高新技术应用于热处理生产中。我国已把环境保护作为一项基本国策,并从1992年开始推进清洁生产技术。根据清洁生产技术的要求,我国现阶段热处理生产的主要控制目标应是少无污染、少无氧化和节能,并应把真空热处理和可控气氛热处理作为热处理行业“九五”期间重点推广应用的清洁生产技术 。
7 热处理生产的自动化和专业化
7.1 计算机和机器人在热处理中的应用
电子计算机在热处理中的应用,包括计算机辅助设计(CAD)、计算机辅助生产(CAM)、计算机辅助选材(CAMS)、热处理事务办公自动化(OA)、热处理数据库和专家系统等,它为热处理工艺的优化设计、工艺过程的自动控制、质量检测与统计分析等,提供了先进的工具和手段。计算机在热处理中的应用,最初主要用于热处理工艺程序和工艺参数(温度、时间、气氛、压力、流量等)的控制,现在也用于热处理设备、生产线和热处理车间的自动控制和生产管理,还有的用计算机进行热处理工艺、热处理设备、热处理车间设计中的各种计算和优化设计。在热处理中引入计算机,可实现热处理生产的自动化,保证热处理工艺的稳定性和产品质量的再现性,并使热处理设备向高效、低成本、柔性化和智能化的方向发展。计算机在热处理中的应用国外已十分普遍,例如,日本一家摩托车厂的热处理车间,有连续式渗碳炉、周期式渗碳炉、连续软氮化炉等共37台设备,从开始送料,到最终产品检验,全部由计算机控制,每班只需要三个人操作,一人在计算机室内负责全部生产、技术和质量管理,一人在现场巡回检查,一人负责产品质量检验,生产效率极高。我国在热处理行业中应用计算机还是近十多年的事情,目前国内研制生产的热处设备已越来越多地引入了微机控制,极大地提高了设备的自动化水平和生产效率。在热处理工艺过程的实时控制、计算机辅助设计、计算机模拟和数学模型的开发应用等方面,也取得了一定的成绩。
机器人在热处理中的应用,可以有效地改善工人的劳动条件,提高产品质量和劳动生产率。目前主要是用来进行自动装卸料。由于热处理的生产环境差、劳动强度较大,也由于热处理生产向自动化、集成化、柔性化的方向发展,因此,今后机器人在热处理生产中的应用将日趋增多。
7.2 热处理生产的专业化
专业化生产是现代工业的基本特征之一,也是促进热处理行业技术进步的一种重要手段。目前工业发达国家的热处理专业化程度已达到80%以上,而且工业越是发达的国家,其专业化水平也越高,而我国只有20%左右。即使这些为数不多的热处理专业厂,也由于组织管理不善,设备利用率较低,新技术、新工艺采用不多,热处理标准贯彻执行不够,能耗较高,产品质量较差。因此,今后要有目的、有重点地扶持一批有条件的热处理厂和车间,使其成为热处理专业厂和协作点。对热处理专业厂要进一步加强管理,积极采用新技术、新工艺、新设备,严格按照标准化、规范化组织生产,形成技术、经济和服务上的优势,充分发挥专业化生产的优越性。此外,热处理工艺材料,如各种淬火介质、渗剂、保护涂料、清洗剂、加热盐、保护气氛和可控气氛的气源等,也要固定生产单位,进行专业化生产,不断提高质量和扩大品种,并尽可能实现规格化、标准化、系列化。
8 小结
(1) 我国的热处理技术已得到了长足的发展,在热处理的基础理论和某些热处理新工艺、新技术研究方面已达到国际先进水平,但在热处理生产工艺和热处理设备方面还存在较大的差距,主要表现在少无氧化热处理应用少、产品质量不稳定、能耗大、污染严重、管理水平低、成本高。
(2) 目前在我国工业生产上大量应用的还是常规热处理工艺,今后仍将占有重要的地位和相当大的比重,但正在日益改进和不断完善。要以少无氧化加热、节能、无污染和微电子技术在热处理中的应用为重点,大力发展先进的热处理成套技术,利用现代高新技术对常规热处理进行技术改造,实现热处理设备的更新换代,全面提高热处理的工艺水平、装备水平、管理水平和产品水平,这对于改变我国热处理技术的落后面貌,赶上工业发达国家的先进水平,将起到积极的促进作用。
(3)加强科研与生产的结合、材料研究与热处理工艺的结合,进一步挖掘材料的性能潜力,促进新材料的发展,使热处理实现“优质、高效、节能、降耗、无污染、低成本、专业化生产”,这是今后热处理技术的重要发展方向。凡是符合这个方向的热处理技术,就会有强大的生命力,获得较快的发展,反之,则将被淘汰。例如,可控气氛热处理、真空热处理、新型化学热处理、离子热处理、激光热处理、流态化热处理等,均能较好地符合上述方向,今后将获得较快的发展和广泛的应用。而盐浴热处理由于耗能高、污染严重,今后将迅速减少,甚至被淘汰。
(4)虽然电子计算机和机器人在热处理中的应用较之在其它工业领域中的应用起步较晚,但随着热处理自动化程度的不断提高,计算机和机器人的应用也将越来越广泛,这是热处理行业现代化的重要标志之一。热处理专业厂和协作网点,是组织热处理生产的一种好形式,也是促进热处理行业技术进步的一种重要手段。因此,实现热处理生产的自动化和专业化,这也是热处理行业发展的必然趋势。
最新评论
暂无评论
发表评论