高频淬火和中频淬火的区别
次浏览
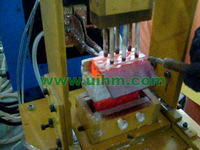
2、中频淬火淬硬层较深(3~
感应加热表面淬火,是利用电磁感应、集肤效应、涡流和电阻热等电磁原理,使工件表层快速加热,并快速冷却的热处理工艺
感应加热表面淬火时,将工件放在铜管制成的感应器内,当一定频率的交流电通过感应器时,处于交变磁场中的工件产生感应电流,由于集肤效应和涡流的作用,工件表层的高密度交流电产生的电阻热,迅速加热工件表层,很快达到淬火温度,随即喷水冷却,工件表层被淬硬
感应加热时,工件截面上感应电流的分布状态与电流频率有关。电流频率愈高,集肤效应愈强,感应电流集中的表层就愈薄,这样加热层深度与淬硬层深度也就愈薄
因此,可通过调节电流频率来获得不同的淬硬层深度。感应加热速度极快,只需几秒或十几秒。淬火层马氏体组织细小,机械性能好。工件表面不易氧化脱碳,变形也小,而且淬硬层深度易控制,质量稳定,操作简单,特别适合大批量生产
常用于中碳钢或中碳低合金钢工件,例如45、40Cr、40MnB等。也可用于高碳工具钢或铸铁件,一般零件淬硬层深度约为半径的1/10时,即可得到强度、耐疲劳性和韧性的良好配合。感应加热表面淬火不宜用于形状复杂的工件,因感应器制作困难
高频感应加热:电流频率在100~500 kHz(千赫),有效淬硬深度为0.5~2 mm(毫米),主要用于要求淬硬层较薄的中、小型零件,如小模数齿轮、中小型轴等。
中频感应加热:电流频率在500~10000 Hz(赫),有效淬硬深度为2~10 mm(毫米),主要用于要求淬硬层要求较深的零件,如中等模数的齿轮、大模数齿轮、直径较大的轴等。
表面淬火零件的中间热处理是调质
表面淬火缺点:处理复杂零件比渗碳困难
常用中碳钢(0.4-0.5%C)和中碳合金结构钢,也可用高碳工具钢和低合金结构钢,以及铸铁。
一般零件淬透层深度为半径的1/10左右时,可得到强度、耐疲劳性和韧性的最好配合。
对于小直径10-20mm的零件,建议用较深的淬透层深度,即可达半径的1/5;
对于截面较大的零件可取较浅的淬透层深度,即小于半径1/10以下。
1,工作于摩擦条件下的零件,如一般小齿轮、轴
45、40Cr、42MnVB;高频淬火,淬深1.5-2mm
2,承受扭曲、压力负荷的零件,如曲轴、大齿轮、磨床主轴等
45、40Cr、65Mn、9Mn2V、球墨铸铁;中频淬火,淬深3-5mm
3承受扭曲、压力负荷的大型零件,如冷轧辊等
9Cr2Mo、9Cr2W;工频淬火,淬深>=10-15mm
表面淬火、普通淬火后碳钢的疲劳强度比较
含碳量% 热处理方法 扭转弯曲疲劳强度
0.33 高频表面淬火 600
0.33 火焰表面淬火 350
0.33 电炉内整体加热淬火 90
0.41 高频表面淬火 600
0.41 电炉内整体加热淬火 110
0.41 正火 130
0.63 高频表面淬火 360
0.63 火焰表面淬火 390
0.63 电炉内整体加热淬火 150
中频感应加热:电流频率在500~10000 Hz(赫),有效淬硬深度为2~10 mm(毫米),主要用于要求淬硬层要求较深的零件,如中等模数的齿轮、大模数齿轮、直径较大的轴等。
表面淬火零件的中间热处理是调质
表面淬火缺点:处理复杂零件比渗碳困难
常用中碳钢(0.4-0.5%C)和中碳合金结构钢,也可用高碳工具钢和低合金结构钢,以及铸铁。
一般零件淬透层深度为半径的1/10左右时,可得到强度、耐疲劳性和韧性的最好配合。
对于小直径10-20mm的零件,建议用较深的淬透层深度,即可达半径的1/5;
对于截面较大的零件可取较浅的淬透层深度,即小于半径1/10以下。
1,工作于摩擦条件下的零件,如一般小齿轮、轴
45、40Cr、42MnVB;高频淬火,淬深1.5-2mm
2,承受扭曲、压力负荷的零件,如曲轴、大齿轮、磨床主轴等
45、40Cr、65Mn、9Mn2V、球墨铸铁;中频淬火,淬深3-5mm
3承受扭曲、压力负荷的大型零件,如冷轧辊等
9Cr2Mo、9Cr2W;工频淬火,淬深>=10-15mm
表面淬火、普通淬火后碳钢的疲劳强度比较
含碳量% 热处理方法 扭转弯曲疲劳强度
0.33 高频表面淬火 600
0.33 火焰表面淬火 350
0.33 电炉内整体加热淬火 90
0.41 高频表面淬火 600
0.41 电炉内整体加热淬火 110
0.41 正火 130
0.63 高频表面淬火 360
0.63 火焰表面淬火 390
0.63 电炉内整体加热淬火 150
下一条: 高频感应加热设备维修怎么办?上一条: 为大家简单介绍一下高频淬火的原理
顶一下
踩一下
最新评论
暂无评论
发表评论